Fiber laser cutting machines six common problem solutions (2) – Catherine
Fiber laser cutting machines six common problem solutions
Any kind of cleavage technique, except for a few conditions that can start from the edge of the board, usually requires a small hole in the board. Previously, in the laser stamping laminating machine, a punch used to punch out a hole. And then the laser used to cut from the opening of the small hole. Fiber laser cutting machine six common problem solutions.
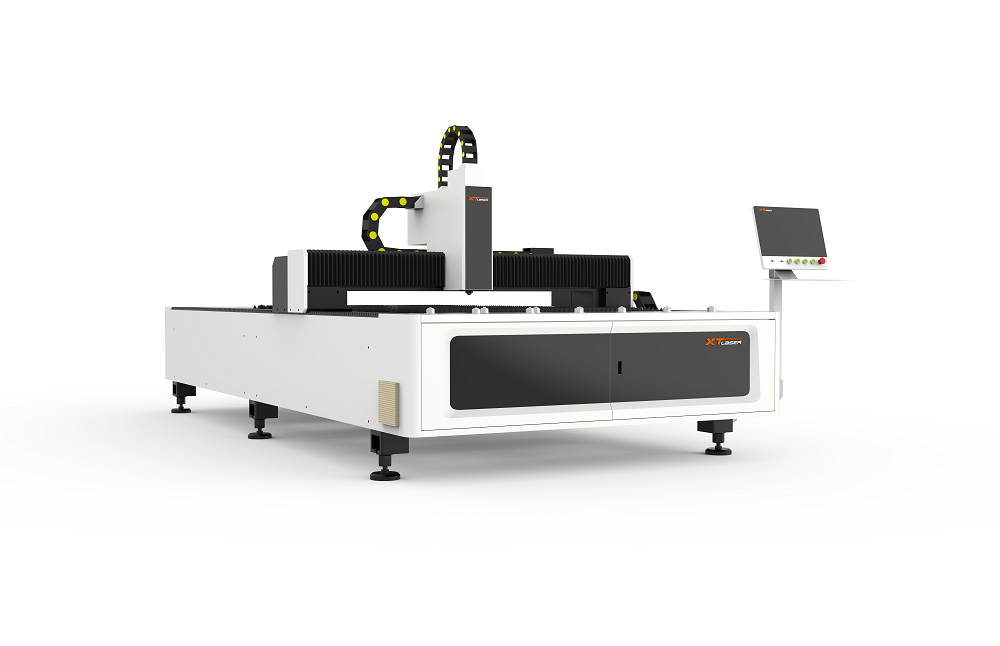
4. A solution to the problem of processing low carbon steel with abnormal sparks
This condition can affect the quality of the cut and the finish of the part. At this moment, if other parameters are normal, the following questions should be considered: 1. Loss of the laser head nozzle? The nozzle should be replaced in time. In the absence of new nozzle replacement, the operating gas pressure should be increased; 2. The thread at the junction between the nozzle and the laser head is loose? At this point, the cut should be immediately suspended to see the laser head connection condition, and the thread is good from the head.
5. Causes of burrs on the workpiece when laser cutting low carbon steel
According to the operation and planning principle of the fiber laser cutting machine, the following reasons are analyzed:
1. The upper and lower directions of the laser focus are not correct. The focus orientation test needs to be performed, and the offset is adjusted according to the focus;
2. The output power of the laser is not good. It is necessary to check whether the operation of the laser generator is normal. If it is normal, investigate whether the output value of the laser control button is correct or not.
3, the line speed of cutting is too slow, you need to increase the line speed when handling;
4, the purity of the cut gas is not good, need to supply high quality cutting gas;
5, the laser focus shift, need to do the focus orientation test, according to the offset of the focus to adjust;
6. The machine is running too long and the instability is present. At this moment, it needs to be shut down and restarted.
6. The laser is not completely cut through
After profiling, it can be found that the following conditions are the primary conditions for processing instability: the selection of the laser head nozzle is not matched with the processing plate thickness; the laser cutting line speed is too fast, and the line speed needs to be reduced during the control; Leading to the laser focus azimuth difference missed, need to detect the nozzle sensing data from the beginning, especially the simplest presentation when cutting aluminum.