How to judge the cutting quality of laser cutting machine
XT Laser-laser cutting machine
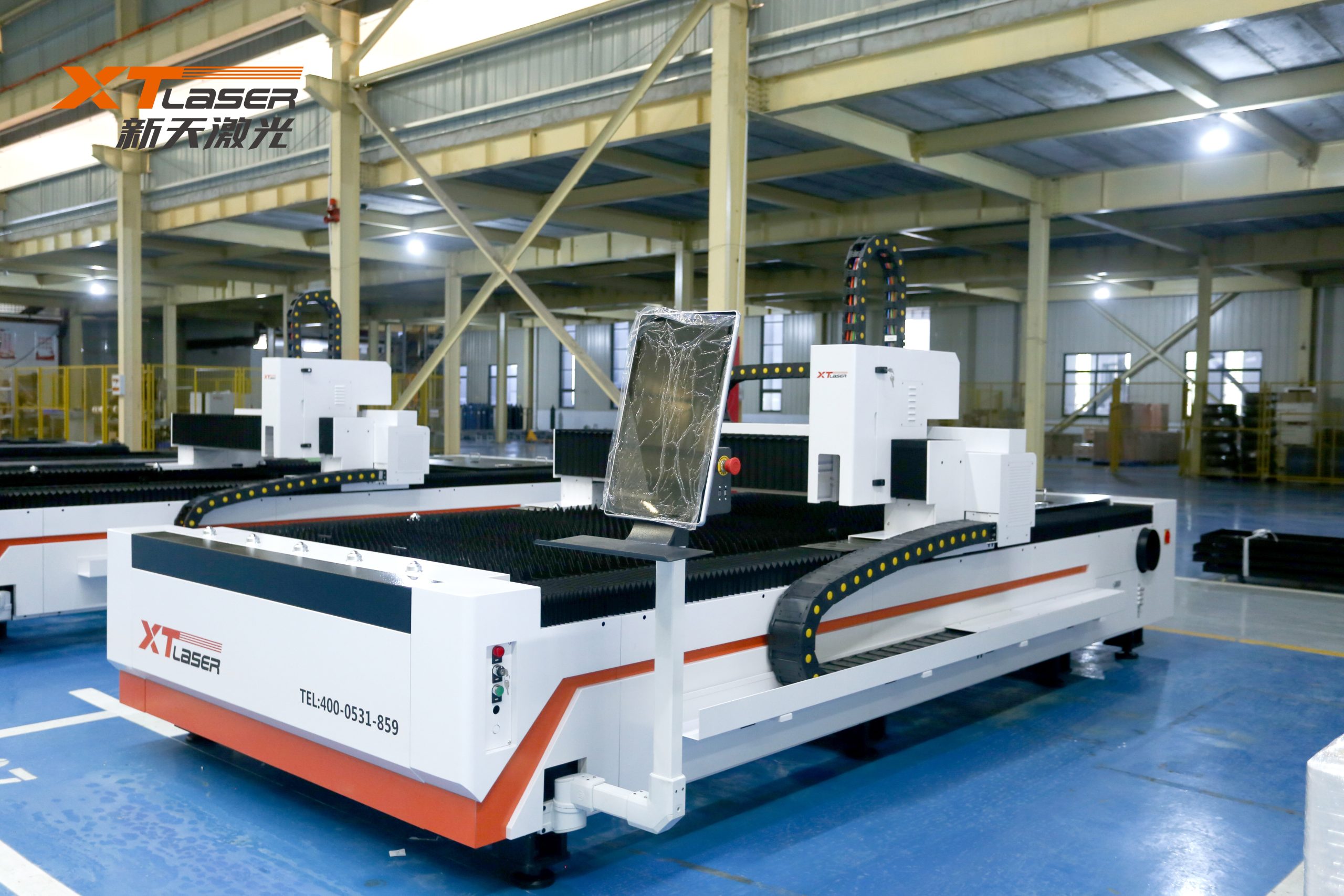
When using laser cutting machine to process metal, sometimes the cutting effect of laser cutting machine is not good and the cutting quality is not in place. This not only wastes materials, but also consumes the vulnerable parts of the laser cutting machine itself. How to judge the cutting quality? What kind of effect is the qualified cutting effect and how to evaluate it. Next, the manufacturer of Xintian Laser Cutting Machine will take you to understand the fiber laser cutting machine and evaluate its processing quality.
1、 Laser cutting machine is used to cut the workpiece with smooth surface, few lines and no brittle fracture.
When laser cutting metal sheet, the trace of molten material will not appear in the incision below the vertical laser beam, but will be sprayed out behind the laser beam. As a result, curved lines are formed on the cutting edge, which closely follow the moving laser beam. In order to correct this problem, using low feed speed at the end of the cutting process can largely eliminate the formation of lines.
2、 Width of cutting gap
Generally, when we use the laser cutting machine for processing, there will occasionally be large cutting gap, which will cause the cutting accuracy of the workpiece to decline and fail to meet the production requirements. What should I do if I encounter such a problem. I came up with three options.
- Check whether there is a problem with the focal length. Pay special attention to cleaning the lens, replacing the focal length of a new lens, and adjusting the correct focal length value.
- Check whether the lens is damaged or dirty, because it will cause laser scattering and cause the laser beam to become larger. The only way is to replace or clean the lens.
- Laser is also a factor that cannot be ignored. Check the laser spot quality. If there are bright spots or spots, holes, holes, etc., the direction should be the support point of the laser. The solution requires adjusting the bracket, rotating direction and replacing the laser.
- Excessive air pressure during oxygen cutting will cause burning of the cutting surface and increase the cutting seam.
- Coaxial misalignment will also cause the notch to become larger.
Large laser cutting seam is not a big problem, but the equipment needs to be maintained after a period of processing and production. In fact, there will be some small exceptions in the use process. This requires us to do a good job in maintenance to ensure the efficient operation of the laser cutting machine and create greater value for users.
Third, the perpendicularity of the slit and the heat-affected zone
Generally speaking, metal laser cutting machines mainly focus on the processing of materials below 5MM, and the verticality of the cross section may not be the most important evaluation factor, but for high-power laser cutting, when the thickness of the processed material exceeds 10mm, the verticality of the cutting edge is very important. When you leave the focus, the laser beam will diverge, and the cutting will expand to the top or bottom according to the position of the focus. The cutting edge deviates several millimeters from the vertical line. The more vertical the edge is, the higher the cutting quality is.
Fourth, no material burning, no molten layer formation, no large slag formation
The slag of metal laser CNC cutting machine is mainly reflected in the deposits and section burrs. Material deposition is due to a special layer of oily liquid on the surface of the workpiece before laser cutting is melted and perforated. Gasification and various materials do not need to be blown down and cut by the customer, but the upward or downward discharge will also form sediment on the surface. The formation of burr is a very important factor that determines the quality of laser cutting. Because the removal of burr requires additional work, the severity and quantity of burr can directly determine the cutting quality. The severity and number of thorns can directly determine the quality of cutting.
5、 Rough plating is carried out on the cutting surface, and the size of surface roughness is the key to measure the quality of laser cutting surface
In fact, for the metal laser cutting machine, the texture of the cutting section has a direct relationship with the roughness. The section texture with poor cutting performance will directly lead to higher roughness. However, considering the differences in the causes of these two different effects, we generally analyze them separately when analyzing the processing quality of metal laser CNC cutting machine. The laser cutting part will form a vertical line. The depth of the line determines the roughness of the cutting surface. The lighter the line, the smoother the cut. Roughness affects not only the appearance of edges, but also the friction characteristics. In most cases, the roughness should be reduced as much as possible, so the lighter the texture, the higher the cutting quality, It will inevitably cause thermal shock to metal materials in the process of use, and its manifestations mainly include three aspects.
- Heat affected zone.
2 Pitting and corrosion.
3 Deformation of materials.
Heat affected zone refers to laser cutting. When the area near the cutting is heated, the metal structure changes. For example, some metals harden. The heat affected zone refers to the depth of the area where the internal structure changes. Pitting and corrosion are harmful effects on the surface of cutting edge and affect the appearance. They occur in cutting errors that should normally be avoided. Finally, if the cutting causes the part to heat up sharply, it will deform. This is particularly important in fine machining, where the profile and web are usually only a few tenths of a millimeter wide. Controlling the laser power and using short laser pulses can reduce the heating of components and avoid deformation.
In addition to the above principles, the state and final shape of the melting layer during processing directly affect the above processing quality evaluation indicators. The surface roughness of laser cutting mainly depends on the following three aspects:
- Internal parameters of the cutting system, such as spot mode, focal length, etc.
- The process parameters in the cutting process can be adjusted, such as power, cutting speed, auxiliary gas type and pressure.
3 Physical parameters of processing materials, such as laser absorptivity, melting point, viscosity coefficient of molten metal oxide, surface tension of metal oxide, etc. In addition, the thickness of the workpiece also has a great impact on the surface quality of laser cutting. Relatively speaking, the smaller the thickness of the metal workpiece, the higher the roughness level of the cutting surface.
Why do most metal processing customers choose optical fiber laser cutting machine now, because it has certain advantages as a representative of advanced productivity.
- It is suitable for all kinds of metal sheet processing, and has certain advantages for metal sheet processing below 20mm.
- Any complex graphics can be processed as long as they are drawn on the computer and input to the control system.
- High cutting accuracy, small thermal deformation, non-contact processing, and basically no secondary polishing treatment on the surface.
- The use cost is low. In the later use, only the basic electricity and auxiliary gas costs are needed.
- It is environmentally friendly, noiseless and has no pollution to the surrounding environment.
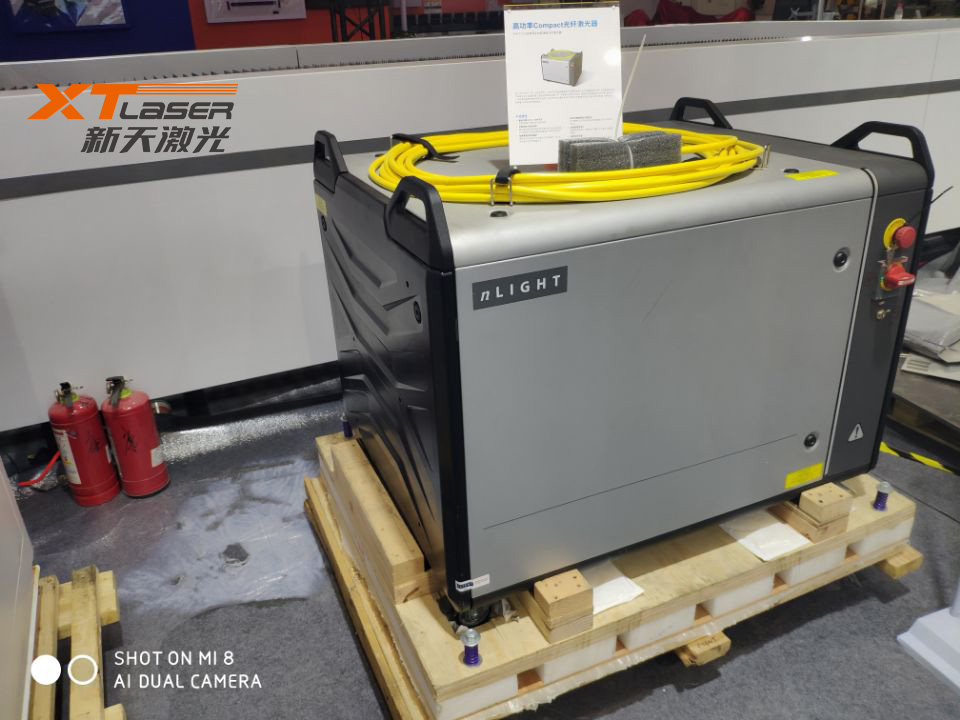