Advantages of laser metal cutting machine
XT Laser-CNC laser cutting machine
With the continuous development and maturity of laser technology, laser equipment has been widely used in all walks of life, such as laser marking machines, laser welding machines, laser drilling machines and laser cutting machines. In particular, CNC laser cutting machinery and equipment have developed rapidly in recent years and are widely used in sheet metal, hardware products, steel structures, precision machinery, auto parts, glasses, jewelry, nameplates, advertising, handicrafts, electronics Toys, packaging and other industries. The significant advantages of laser cutting machine compared with other cutting equipment are mainly reflected in the following aspects:
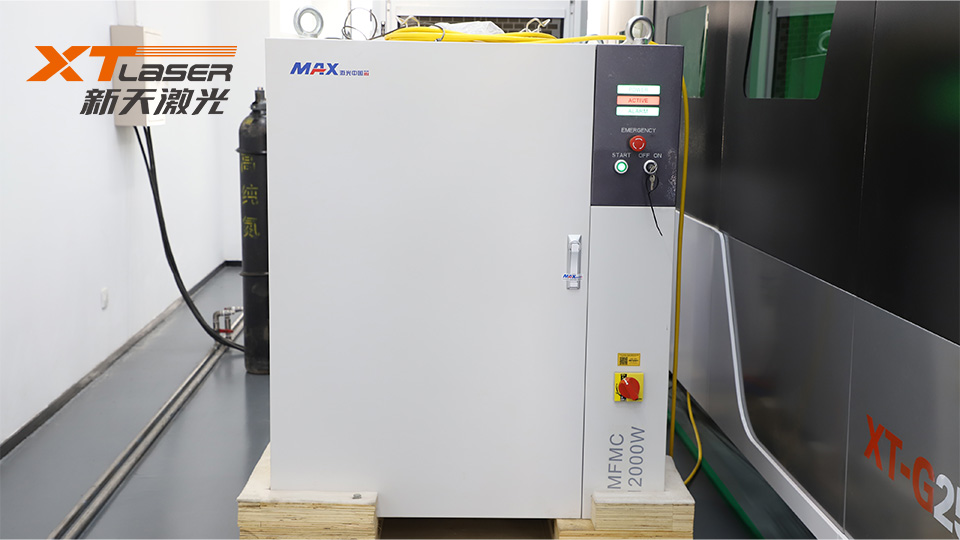
1. Fast cutting speed, good cutting quality and high precision;
2. The cutting seam is narrow, the cutting surface is smooth, and the workpiece is not damaged;
3. It is not affected by the shape of the workpiece and the hardness of the cut material;
4. In addition to processing metal materials, nonmetals can also be cut;
5. Save mold investment, save materials and save costs more effectively;
6. It is easy to operate, safe, stable in performance, and can improve the development speed of new products. It has wide adaptability and flexibility.
CNC metal laser cutting equipment frame is the most important part of the laser equipment. Not only are most parts installed on the frame, but also bear the gravity of the workbench and all inertial impact loads during acceleration and deceleration.
The design and R&D work of the laser cutting machine frame mainly includes:
1. Determine the conditions for rapid, high-precision and stable operation of CNC laser cutting equipment under various working conditions and environments.
2. The structure and parameters of the frame are determined according to the functional requirements, and the corresponding dynamic model is established according to the structural characteristics of the laser cutting machine.
3. The influence of frame structure and parameters on the static and dynamic stiffness and thermal stability of the frame is studied, and the theoretical basis for frame design is provided.
4. Determine the coupling relationship between the rack and other components.
Therefore, in the design of the frame of the laser cutting machine, how to reasonably arrange the metal, reduce the dead weight, improve the rigidity of the body, and reduce the impact of temperature changes on the accuracy are the key issues to be considered in the design process.
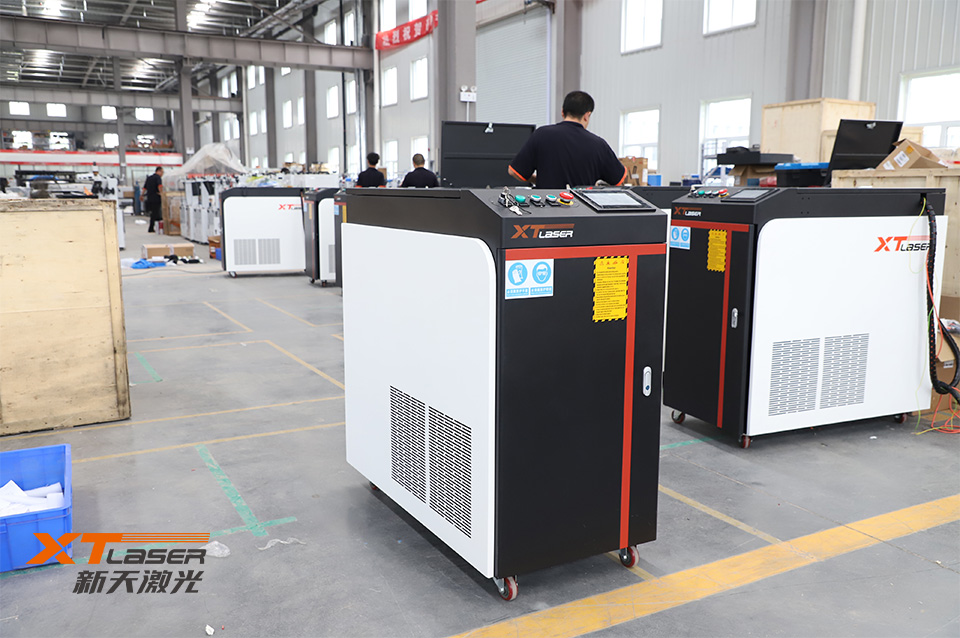
In the actual circuit of laser cutting machine, there is a problem of strong electrical interference between analog signal and digital signal. The function of the photoelectric isolation circuit is to transmit signals with light as the coal medium under the condition of electrical isolation, so that the input and output circuits can be isolated. Therefore, it can effectively suppress the system noise, eliminate the interference of the grounding circuit, and has the advantages of fast response speed, long life, small size and impact resistance, making it widely used in the strong-weak current interface, especially in the forward and backward channels of the microcomputer system.
Photocoupler has three characteristics:
1. The signal transmission takes the form of electric-optical-electricity, and the light-emitting part and light-receiving part are not in contact, which can avoid the feedback and interference that may occur at the output end to the input end;
2. Strong ability to suppress noise interference;
3. It has the advantages of durability, high reliability and fast speed. The response time is generally within a few, and the response time of high-speed optocoupler is even less than 10ns.
Therefore, when designing the circuit of the laser cutting machine system, attention should be paid to the isolation of the input signal circuit when connecting with the single chip computer. Here, photoelectric coupling is the most commonly used method.
In the metal processing industry, which plays a very important role in the industrial manufacturing system, many metal materials, regardless of their hardness, can be cut without deformation. Of course, for materials with high reflectivity, such as gold, silver, copper and aluminum alloys, they are also good heat transfer conductors, so laser cutting machines are very difficult, or even unable to cut.
Although the laser cutting machine technology has obvious huge advantages, as a high-tech equipment, in order to use the laser cutting machine to achieve the ideal cutting effect, it is also necessary to master its processing technical parameters and operating procedures. Especially in the cutting process of laser cutting machine, it is necessary to select the appropriate cutting speed, otherwise it may cause several bad cutting results, mainly as follows:
1. When the laser cutting speed is too fast, the following adverse results will be caused:
① Method of cutting and random spark spraying;
② Cause the cutting surface to present oblique stripes, and the lower part to produce molten stains;
③ The whole section is thick, but there is no molten stain;
2. On the contrary, when the laser cutting speed is too slow, it will cause:
① Cause over-melting and rough cutting surface.
② The slit widens and dissolves completely at the sharp corner.
③ Affect cutting efficiency.
Therefore, in order to make the laser cutting machine better play its cutting function, we can judge whether the feed speed is appropriate from the laser equipment cutting sparks:
1. If the spark spreads from top to bottom, it indicates that the cutting speed is appropriate;
2. If the spark tilts backward, it indicates that the feed speed is too fast;
3. If the sparks are not diffused and few, and agglomerate together, it indicates that the speed is too slow.
Most organic and inorganic materials can be cut by laser. Laser cutting technology has obvious advantages over other traditional cutting methods. The laser cutting machine not only has the main characteristics of narrow cutting seam and small workpiece deformation, but also has the characteristics of fast speed, high efficiency, low cost, safe operation and stable performance.