Summer Maintenance Tips for Fiber Laser Cutting Machine
In the scorching summer, the fiber laser cutting machine is still in continuous operation. The price of the laser cutting machine is high, and protective measures need to be taken. As the temperature rises, customers must take preventive measures. Proper maintenance of the laser cutting machine is crucial to effectively avoid damage to the laser generator, improve work efficiency, and extend the service life of the machine.
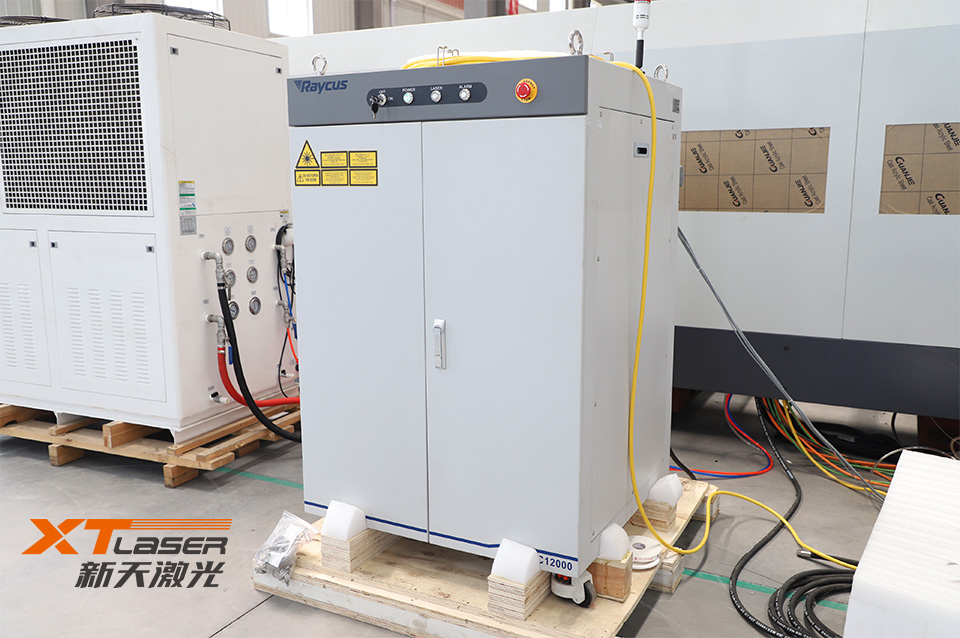
Starting from the following perspectives:
The temperature of the cooling water should not differ too much from the temperature of the air. The laser and optical lenses of the laser cutting machine both use water cooling methods. Due to the condensation of water in the air when cooled, when the temperature of the cooling water is below 5-7 degrees Celsius, there will be water condensation on the surface of the laser and optical lenses, which greatly affects the output efficiency of the laser and the transparency of the optical lenses, and has a significant impact on the laser energy and the service life of optical accessories. Separate water cooling is recommended for multiple parts of the laser and cutting head. Users are advised to set the temperature of the laser’s low-temperature water circuit to around 26 degrees Celsius, and the temperature of the cutting head and fiber optic water circuit to around 30 degrees Celsius (depending on temperature and humidity values),
Strictly adhere to the summer switch on/off sequence.
Startup sequence:
1. Turn on the main power supply of the laser and key on the tube;
2. Wait for two hours;
3. Turn on the chiller.
Shutdown sequence:
1. Turn off the chiller;
2. Turn off the laser.
Warning:
It cannot appear that the laser has been turned off,
The chiller is still running!
Wet and hot weather can cause laser power supply and
Moisture or condensation occurs in various parts of the laser equipment,
This leads to various malfunctions occurring,
This seriously affects the normal production of users.
Faults caused by the above reasons,
Not within the normal warranty scope.
be careful:
1. When the laser equipment is shut down, the water cooler should also be turned off to prevent condensation caused by excessive temperature difference during shutdown;
2. We strongly request customers in the integrated operation room to install air conditioning or install lasers in the air conditioning room, and to maintain continuous and stable operation of the air conditioning (including in the evening) to maintain indoor temperature and humidity. Alternatively, each time the air conditioning is turned on, it should be turned on for half an hour before turning on the laser equipment power and chiller.
Rail maintenance
The guide rail should be regularly cleaned to remove dust and other debris, ensuring that the transmission part of the equipment is lubricated and free of debris. Regular cleaning and lubrication can ensure precise positioning of the machine during operation, achieving more accurate cutting and improving product quality. As the temperature increases in summer, the working pressure of the cooling system of the laser cutting machine increases. It is recommended to check and maintain the internal pressure of the cooling machine before the high temperature arrives. The pressure of equipment from different manufacturers also varies. It is recommended to consult the equipment manufacturer for specific parameters before maintenance. Due to the high temperature in summer, the deterioration rate of cooling water will also accelerate. It is recommended that users use regular distilled or purified water, regularly clean the water tank scale and replace the water and filter element (it is recommended that the replacement cycle in summer should not exceed 15 days), to avoid causing scale to adhere to the laser and pipeline, affecting the cooling water flow and causing a high temperature alarm,
Method for cleaning scale
Please operate under the guidance of the equipment manufacturer.