How to solve the burr problem of metal laser cutting machine
XT Laser-laser cutting machine
There are many applications of laser cutting machine in metal material processing. Because of its high efficiency and high cutting quality of finished products, it has become the standard configuration of metal plate processing station. Metal laser cutting machine is the largest market in the laser cutting machine industry.
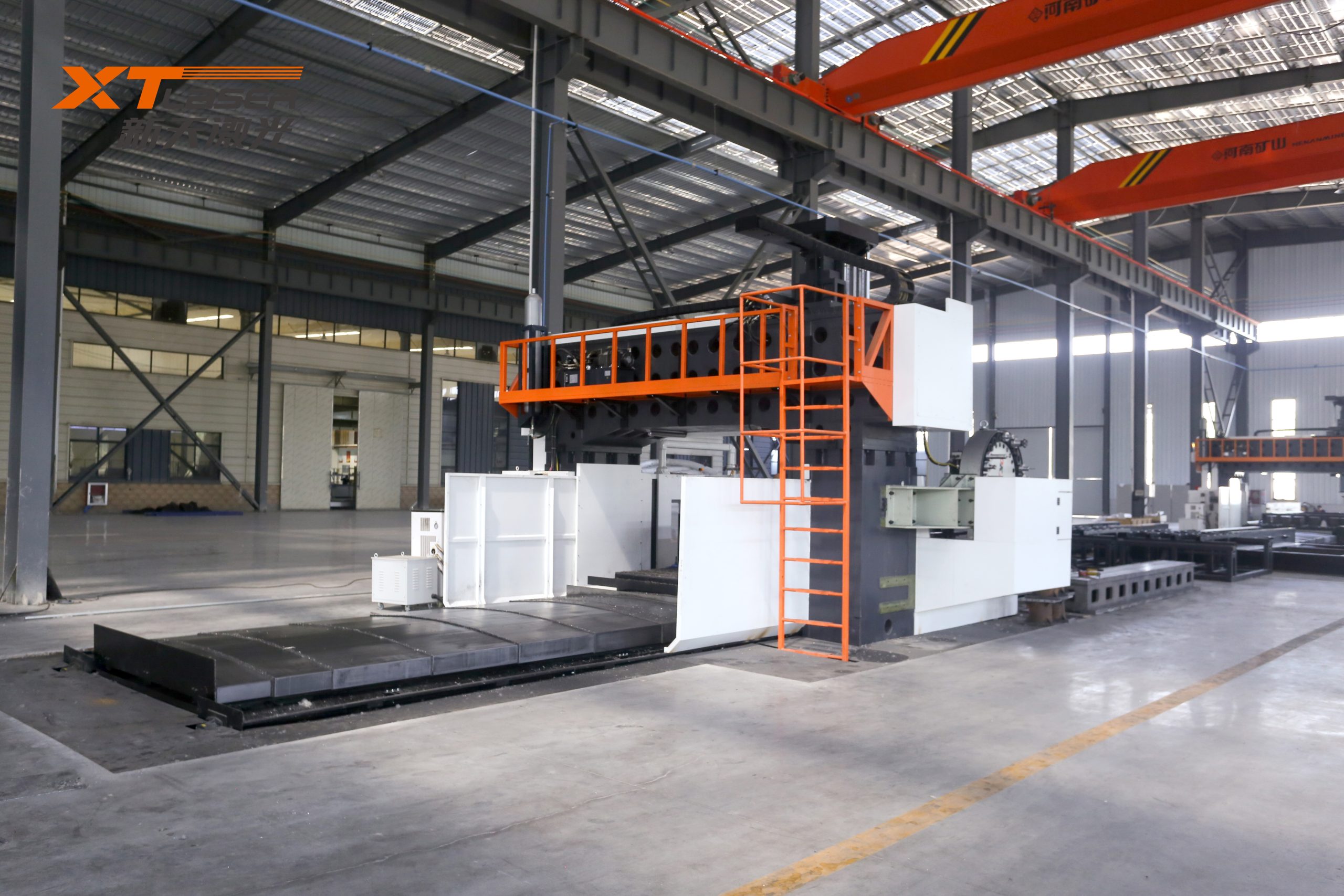
However, when some customers use laser cutting, there are many burrs on the front and back surfaces of the sub-material. These burrs will not only affect the work efficiency of the production team, but also need to inject more human resources to participate in the grinding of the rough edges, which is time-consuming and laborious.
When this situation occurs, it is not the problem of the cutting machine itself as people think, but the improper operation.
In the process of plate processing, the purity of auxiliary gas of laser cutting machine and the setting of cutting process data parameters will affect the processing quality.
So what is the burr?
In fact, burr is the residual particles melted and re-solidified on the surface of metal materials – the energy generated by laser beam focusing on the surface of the workpiece vaporizes and blows out the slag.
Due to improper subsequent operation, the molten substance was not removed in time and “hung on the wall” on the surface of the sub-material.
1. Auxiliary gas — pressure and purity
The auxiliary gas has the function of blowing out the slag in the cutting groove on the surface of the workpiece after the material in the cutting trace of the sub-material is melted. If the gas is not used, the burr will be generated after the slag is cooled.
Therefore, the gas pressure should be sufficient and appropriate (too small to blow clean — adhesion, cutting; too large to melt — large section grain, twill). The pressure varies with the plate, and the appropriate pressure can be found through the proofing test.
In addition, the auxiliary gas should be pure, which leads to the reduction of the speed of the laser head running on the surface of the workpiece (the auxiliary gas can not produce sufficient chemical reaction with the sub-material 100%),
The speed becomes slow, and the incision is rough or even cannot be cut through.
In addition, according to the inquiry of relevant data, the appropriate change law of auxiliary air pressure is: when oxygen (auxiliary gas) is used to cut carbon steel plate: when the thickness of the sheet increases from 1mm to 5mm, the cutting pressure range decreases to 0.1-0.3MPa, 0.1-0.2MPa, 0.08-0.16MPa, 0.08-0.12MPa, 0.06-0.12MPa in order;
When the thickness of medium and thick carbon steel plate increases from 6 mm to 10 mm, the corresponding auxiliary gas – oxygen pressure range decreases to 0.06-0.12 MPa, 0.05-0.10 MPa and 0.05-0.10 MPa in turn; When cutting stainless steel plate with nitrogen (auxiliary gas): when its thickness increases from 1mm to 6mm, the cutting pressure changes from 0.8-2.0MPa to 1.0-2.0MPa to 1.2-2.0MPa, which is high pressure cutting.
2. Parameter setting – focus position, cutting lead-in position When the customer has prepared the laser cutting machine, it is better to let the experienced operator debug the equipment.
Therefore, the cutting parameters should be adjusted as much as possible. The air pressure, flow rate, focal length and cutting speed should be adjusted several times. The parameters provided by the machine cannot cut high-quality workpiece.
Too high the focus position will make the burr “swell”, and the burr is very hard and the side is not smooth. It also requires multiple debugging to find the focus position.
The lead-in wire should be properly away from the sub-material to prevent local overheating, and the “molten lump” on the back of the sub-material. The lead-in line is relative to the run-on hole.
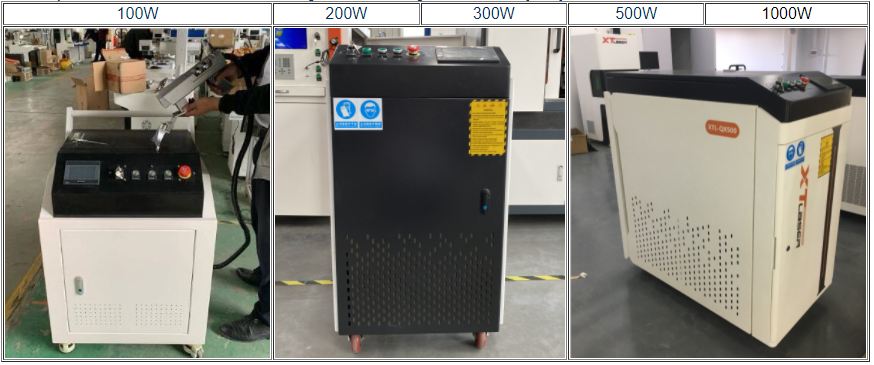
The arc striking hole is also called “cutting starting hole”. The diameter of the arc striking hole is larger than the normal cutting seam. Therefore, in order to improve the cutting quality and save the sheet metal, the arc striking hole should be placed at the sheet metal scrap and cut not reliably close to the part contour. And the lead-in line is introduced in two ways: straight line and arc.
For example, the parameters of laser cutting machine cutting stainless steel lead-in wire.
1. When cutting 1-3 mm stainless steel, use a single (small circle or deceleration) method.
2. When cutting 3-6 mm stainless steel, adopt two methods (cutting small circle or reducing speed).
3. The air pressure for cutting small circle is 1.5 times higher than that for cutting.
In general, when burrs appear on the front and back surfaces of the sub-material, they can be checked and solved from the following aspects:
1. The focus of the beam deviates from the upper and lower positions.
2. The output power of the laser cutting machine is not enough.
3. The wire cutting speed of the cutting machine is too slow.
4. The purity of auxiliary gas is not enough.
6. Fatigue operation of laser cutting machine.
Optical fiber laser cutting is a precise cutting method, and often a data error will cause its abnormal operation, so it should be strict in work to reduce errors.